Concreter’s Hand Partially Amputated After Incident on Melbourne Construction Site
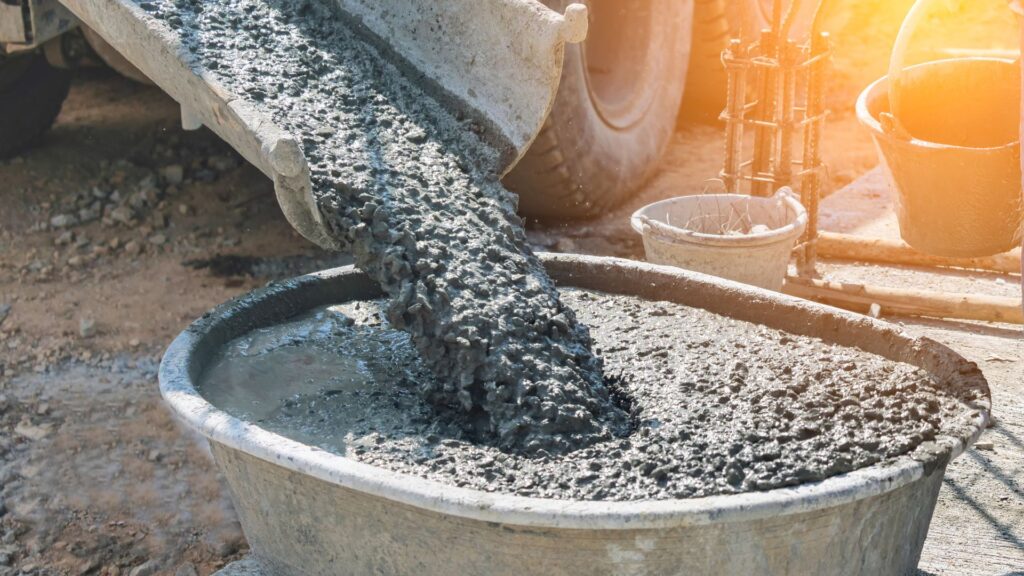
A tragic incident on a Malvern construction site has resulted in a Melbourne concreter losing half his hand due to faulty equipment.
In April 2022, a worker was setting up a truck-mounted pump when a hydraulic interlock valve failed to activate, causing a swing tube inside the hopper to trap and partially amputate his right hand. The valve was supposed to shut off the pump when the safety grate was lifted, but it did not function as intended. Despite being instructed by WorkSafe to preserve the scene for investigation, the sole director of TP Structures moved the truck back to a storage yard, leading to further legal consequences.
The Outcome: Legal Ramifications and Emphasis on Safety
On August 6, 2024, TP Structures was sentenced in the Moorabbin Magistrates’ Court, pleading guilty to charges of failing to provide a safe work system and disturbing the site of a notifiable incident. TP Structures has been convicted and fined $30,000 following the incident, with an additional $5,673 in costs. The court emphasised that the accident could have been prevented through simple daily pre-operation checks, which would have identified the faulty valve before the machinery was used.
The Need for Digital Plant & Equipment Safety Tools
In today’s construction industry, digital tools have revolutionised how head contractors and subcontractors manage the safety and compliance of plant and equipment on site. These tools allow for comprehensive health checks, tracking of service histories, and streamlined registration processes, all of which are crucial for maintaining a safe working environment.
For example, modern platforms like 1Breadcrumb enable subcontractors to easily induct their plant and equipment to a site using a smartphone, providing instant access to essential information such as serial numbers, risk assessments, manuals, and logbooks. Contractors can manage their own equipment, ensuring it meets safety standards and is ready for use.
These tools also offer complete visibility into the equipment’s status on each project, whether from the office or on-site. They allow for tracking the location, usage history, and certification of operators, ensuring that only licensed and certified personnel are operating machinery. Additionally, equipment can be moved freely between sites, with unique identifiers like barcodes or QR codes attached for quick location and auditing, helping contractors maintain oversight and safety across multiple projects.
Recent Comments